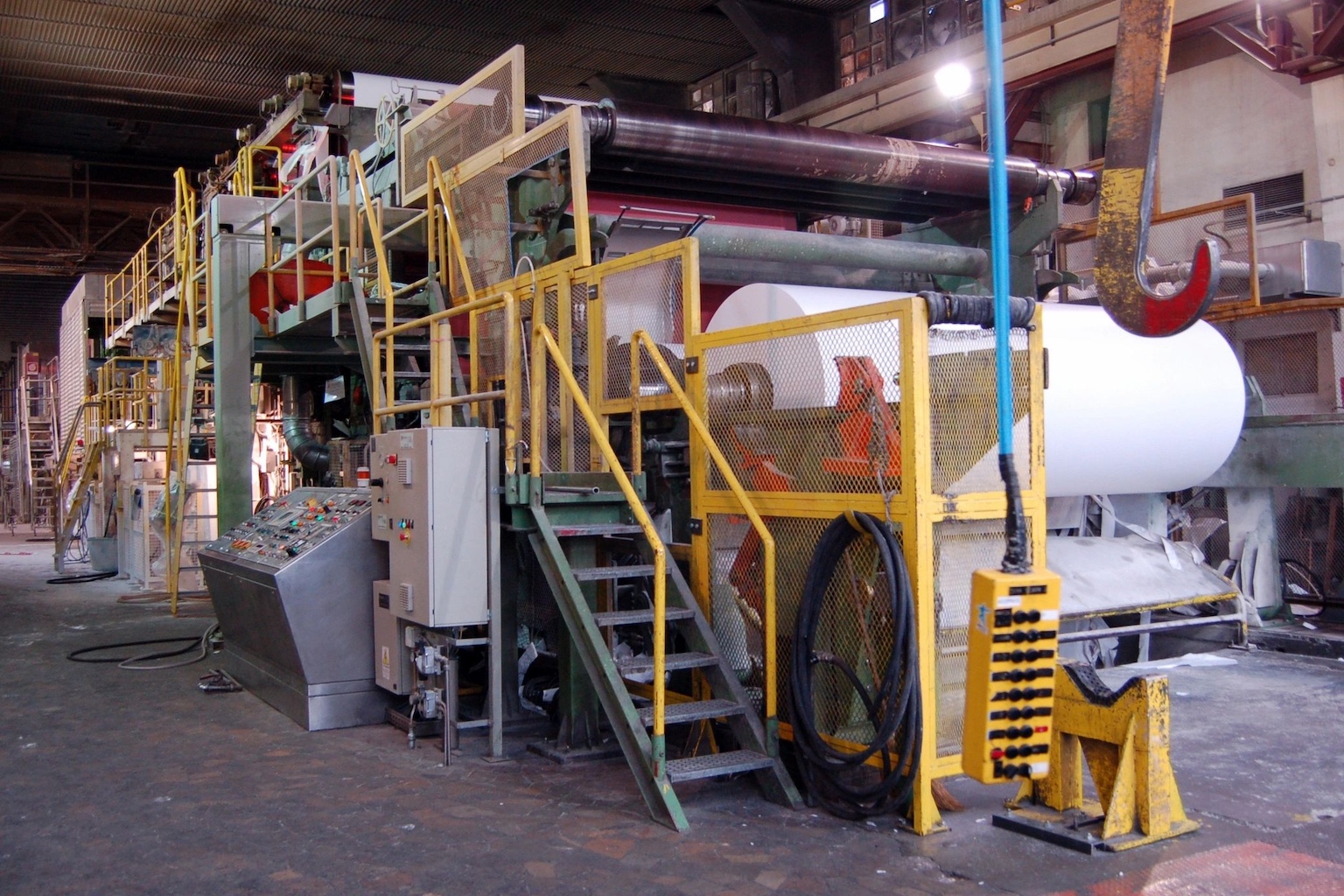
Case Study: Neenah, Inc. Implements Shop Floor Solution to Increase Productivity
Introduction
Neenah, Inc. (now Mativ) faced challenges in enhancing productivity and efficiency. To address these, they implemented RedHawk Shop Floor, a solution designed to optimize shop floor operations and provide real-time data insights. This case study explores the journey and results achieved through this implementation.
Challenges
Neenah aimed to excel in productivity and performance, analyze broke and waste, gain insight into inventory transactions, and implement Six Sigma and LEAN initiatives. They needed executive-level information and real-time shop floor data to improve process flow, manufacturing efficiency, and provide accountability.
Solution
In January 2015, Neenah implemented RedHawk Shop Floor in their Finishing facility in Whiting, WI. The solution included several key components:
- Shop Floor Management: This module was designed to manage order production efficiently. It allowed operators to print labels and create material seamlessly, ensuring that production processes were streamlined and error-free.
- Reporting Dashboard: The dashboard provided a comprehensive view of running orders through the Live Feed feature. It also offered detailed reports on operation trends, goals, and yield comparisons, enabling managers to make informed decisions based on real-time data.
- Data Integration: RedHawk Shop Floor integrated with existing systems to ensure that all relevant data was captured and analyzed. This integration facilitated better inventory management and provided insights into broke and waste analysis.
- User Training and Support: The solution included extensive training for operators to ensure they were proficient in using the software. Continuous support was provided to address any issues and optimize the use of the system.
Implementation
The implementation of RedHawk Shop Floor was carried out in a phased approach to ensure smooth transition and minimal disruption to operations:
- Phase 1: Initial Setup: In January 2015, the initial setup of RedHawk Shop Floor began. This phase involved configuring the software to align with the company’s specific needs and integrating it with existing systems.
- Phase 2: Operator Training: Training sessions were conducted for operators to familiarize them with the new system. By April, operators were confident in using the software, which provided total accountability for time, product, efficiency, broke, and shift data.
- Phase 3: Monitoring and Optimization: Continuous monitoring was carried out to ensure the system was functioning optimally. Feedback from operators was used to make necessary adjustments and improvements.
- Phase 4: Full Deployment: By mid-2015, RedHawk Shop Floor was fully deployed across the Finishing facility. The system was now providing real-time data and insights, enabling managers to make informed decisions and improve process flow.
Results
Within six months, Neenah observed significant improvements:
- Increased Run Time: The machine’s run time increased by 7% by June.
- Increased Uptime: Uptime increased by 5% by May and 7% by June.
- Improved Maintenance Procedures: Maintenance procedures were enhanced.
- Decreased Changeover Time: Changeover time decreased by 23%, saving 22 hours in May alone.
- Increased Rate of Operation: The rate of operation increased by 15% from April to June.
- Estimated Savings: Over $100,000 in annual cost savings from one machine.
Expansion
Following the success at the Finishing facility, Neenah decided to expand the use of RedHawk Shop Floor to other locations:
- Additional Machines at Finishing Facility: The solution was installed on additional machines at the Finishing facility. This expansion ensured that the benefits observed on the initial machine were replicated across other machines, further enhancing productivity and efficiency.
- Deployment at NewLocation: RedHawk Shop Floor was also implemented at several machines at another location. This deployment aimed to standardize operations across different facilities and leverage the insights gained from the initial implementation.
- Continuous Improvement: The company continued to monitor and optimize the use of RedHawk Shop Floor, ensuring that the system evolved to meet changing needs and challenges. Regular training sessions and support were provided to operators at all locations.
Conclusion
Neenah’s implementation of RedHawk Shop Floor led to substantial productivity gains, improved maintenance procedures, and significant cost savings. The solution provided real-time data, accurate problem diagnosis, and improved process flow, contributing to the company’s continuous improvement plan.